xuebaunion@vip.163.com
3551 Trousdale Rkwy, University Park, Los Angeles, CA
留学生论文指导和课程辅导
无忧GPA:https://www.essaygpa.com
工作时间:全年无休-早上8点到凌晨3点
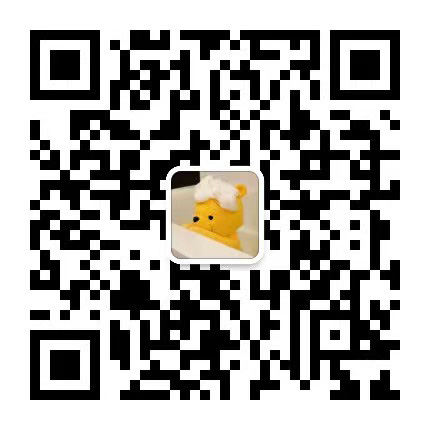
微信客服:xiaoxionga100
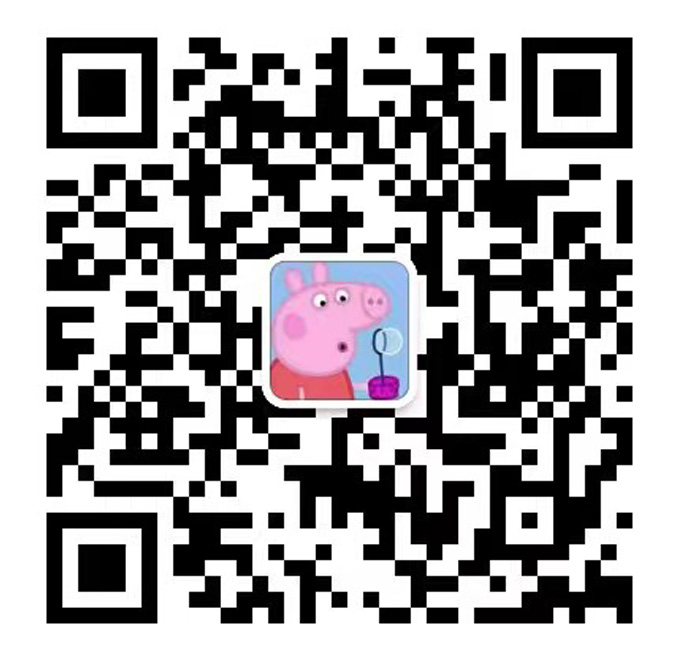
微信客服:ITCS521
MIET1077 Supplementary Material 1 Introduction This document aims to elaborate on the video explanation provided by Prof Firoz Alam in regards to the six-bar linkage mechanism, which is relevant to what students need to do for their second major assessment. The first part provides a brief summary of the fundamentals discussed in the video; the second part provides a guide on how to build the mechanism using the simulation software: Working Model. A rigid body can have three types of motion: 1. Translational/Curvilinear 2. Rotational 3. General plane (combination of curvilinear and rotational motion) Identifying of links on a six-bar linkage mechanism When counting linkages, a ground is always considered Link 1 as it provides a fixed point (or anchor) for the mechanism. A mechanism can have multiple grounds so only one of them would be considered ‘link 1’. The naming order in the video is as follows: Figure 1. The naming order applied as per the explanation video. Upon inspection, the motions produced by each link can be summarised as follows: • 2 x ‘pin’ Ground (provides rotational motion; ground on the left is considered Link 1) • 1 x ‘slider’ Ground (provides translational motion) • Link 2: rotational motion (in relation to a Ground) • Link 3: general plane/complex motion (in relation to Link 2, 4 and 5) • Link 4: partial rotational motion (in relation to a Ground) • Link 5: general plane/complex motion) • Link 6: translational/linear motion (in relation to a Ground) In real-life scenarios (e.g. car engines), it is of utmost importance to be able to associate the correct motion generated by each link, in order to achieve dynamic balancing of forces within the overall system. MIET1077 Supplementary Material 2 Recreating the Linkage Mechanism based on Relative Positions The purpose of this reference guide is to provide students with the basic understanding in how to reconstruct a simulation model using a computer software, which students will need to be able to do for their second assignment. While we are using Working Model, the principles and logic used here should be applicable across any other modelling software that students decide to use (e.g. Solidworks, PTC Creo or AutoCAD Inventor etc.). A difference to note in this example is that, as we do not have the actual measurements for the model, we will need to attempt to reconstruct the model based on relative distances. However, sufficient parameters will be provided to build the model for your assignment and so this first step will not be necessary. Step 1: Establish a unit of measurement Any software that allows a ‘grid view’ mode with standardised units will do. In this case, MS Powerpoint is used with the grid spacing set to 1cm : 1cm. The colour of the original image was adjusted to make the grid more visible while preserving sufficient contrast of the linkage mechanism for determining the relative distance. Figure 2. Image of the mechanism showed in the video demonstration labelled with relative dimensions. MIET1077 Supplementary Material 3 Step 2: Approximate angles of links relative to their respective grounds Once the relative distances are determined, angles of the links can be approximated as illustrated below: Figure 3. Approximation of dimensions and angles of the mechanism. Step 3: Setup of the Working Model software Enable the grid lines for ease of referencing; the option can be found in the ‘Workspace’ under ‘View’; also change the default angle from ‘radians’ to ‘degrees’. Figure 4. Setup of the Working Model program’s ‘Workspace’ by enabling dimensional options like ‘Grid Lines’. MIET1077 Supplementary Material 4 Figure 5. Setup of the Working Model program by changing the default from radians to degrees. Step 4: Recognising with the tools required to construct the mechanism The following are the tools needed for this project. Figure 6. Label of the tools needed to recreate the six-bar linkage mechanism. The different shapes (circle, polygon and rectangle) are used to form different parts of the mechanism including the various grounds and links. The anchor is used to define fixed/immobile parts of the mechanism—i.e. the grounds. The pin joint connects objects together and provides rotational motion; the keyed slot joint connects objects together and provides translational motion by defining the ‘back object’ as the path for the ‘front object’. When the joint is inserted onto overlapping objects, the track of the joint will be always be added on to the back object. Objects inserted later will always be considered as ‘in front’ relative to objects that have been inserted earlier, and will appear on top when placed over another object. MIET1077 Supplementary Material 5 Figure 7. Example of a keyed slot joint mechanism as drawn in Working Model. This can be changed by first selecting an object, then go to the Object menu and click on the ‘Move To Front’ or ‘Send To Back’ option. Figure 8. Screenshot illustrating the ‘Move To Front’ and ‘Send To Back’ option. The motor provides the mechanism with a directional force allowed by the joint where the motor is placed. In this case, it will be placed on Link 1 to recreate the movement shown in the demonstration video. Step 5: Use the shape and joint tools to create the mechanism Referring back to the Figure 1, the rectangle shape will be used to represent the links and the translational ground (Link 6), the circle shape will be used to represent the circular grounds (Link 1 and 4). The relative positions of the different links are drawn and placed as per determined in Step 1 and 2. The colours of the shapes can also be changed by accessing the ‘Appearance’ menu under ‘Window’. Figure 9. Screenshot illustrating the colour pallets option. MIET1077 Supplementary Material 6 The sizes of shapes can also be adjusted to provide a clearer representation of the mechanism. The easiest way to set the angles is by inserting the shape parallel to the horizontal axis then adjust the angle as per determined from Figure 3. Figure 10. Screenshot of change in angles of shapes. When all the grounds and Link 2, 4, 5 and 6 have been drawn as shown in Figure 11, Link 3 can be easily made using the polygon tool and then selecting the edges of Link 2, 4 and 5 (Figure 12). Figure 11. Illustration of the six-bar mechanism with Link 3 remaining. Figure 12. Drawing of Link 3 using the Polygon tool. Once outlook of the mechanism is complete, anchors are to be added onto the grounds by selecting the anchor icon—it does not matter where the anchor is placed on the shape as long as it is within the shape. MIET1077 Supplementary Material 7 Subsequently, add a keyed slot joint with Link 6 on top of the translational ground and then add a pin joint connecting Link 5 to Link 6. Thereafter, add one pin joint to Links 1, 2, 3, 4 on the ends of the rectangles. Finally, add a motor on top of the pin joint of Ground 1/Link 1. Figure 13. Illustration of the completed model. Step 6: Running the simulation and recording the motion of the links Once all of the anchors, linkages and motor have been added, the simulation of the mechanism can be performed by clicking the ‘Run’ button. The motion of the different links can be plotted by first selecting the link of interest—for example, Link 2 as shown below—and then choose ‘X Graph’ under the ‘Measure’ tab and ‘Position’ subtab (Figure 14). Figure 14. Insertion of a position plot for a specific link. The plot measures time vs x-position as its default setting, which produces a sinusoidal waveform (Figure 15). The graph can be edited so that both the x and y positions are captured to illustrate the link’s movement path. The ‘Properties’ window of the plot can be accessed by double-clicking the on the graph. MIET1077 Supplementary Material 8 Figure 15. Adjusting the default plot from time vs x-position. To change the plot, replace the ‘t’ with ‘x’ and ‘time’ with ‘Body[7]p.x’, and ‘x’ with ‘y’ and ‘Body[7]p.y’, so that the graph will now plot the x and y positioning of the link—relative to the coordinate system of the program. Note that the ‘Body[X]…’ portion may be different depending on the order of which the shape was inserted. To enlarge the graph, the maximum and minimum values of the x and y axis can be adjusted accordingly by going back to the ‘Properties’ window (Figure 16). Figure 16. Adjustment of the maximum and minimum values of the plot to increase the resolution. Once all of the adjustments have been done, rerun the simulation to ensure the model and plot are operating as expected. MIET1077 Supplementary Material 9 Figure 17. Model of the linkage mechanism after running the simulation with position plot included.