xuebaunion@vip.163.com
3551 Trousdale Rkwy, University Park, Los Angeles, CA
留学生论文指导和课程辅导
无忧GPA:https://www.essaygpa.com
工作时间:全年无休-早上8点到凌晨3点
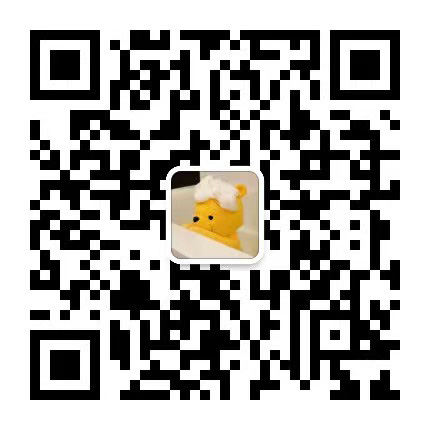
微信客服:xiaoxionga100
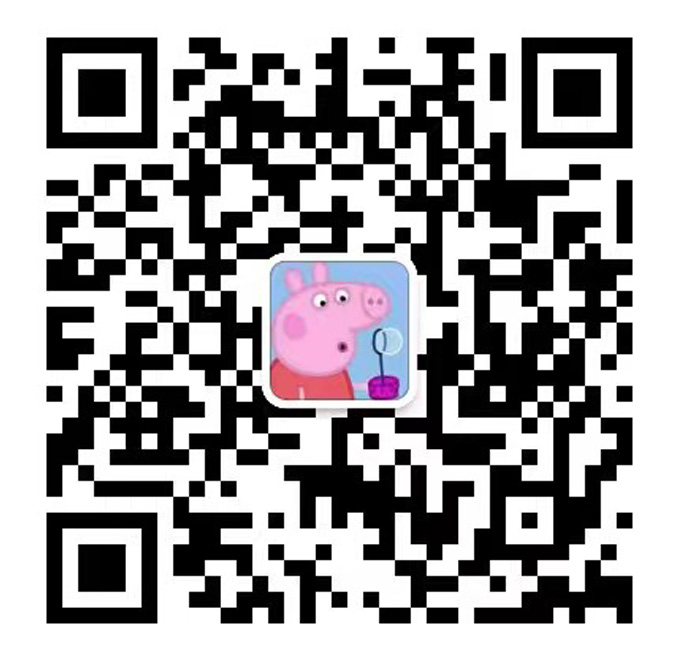
微信客服:ITCS521
CIV350 Geotechnical Design Coursework 21/22 CIV350 Geotechnical Design Coursework Anchored Sheet Pile Wall Design Project 1 Problem Description The sides of a 9.0m deep excavation in sand are to be supported by an anchored sheet pile wall as shown in Figure 1.1. An example LimitState:GEO file: ‘anchored wall example.geo’ is available for download (see later) and may be used and adapted for this coursework. It is up to you to adapt this model and ensure that the parameters are as required for the specified design. Ensure you read the notes (see later) regarding the modelling in LimitState:GEO. Figure 1.1: Anchored sheet pile wall problem Your task is broken into two parts, the first is to determine the baseline design, the second is to look at the effects of parameter/assumption variation: Part I: Baseline design Your task is to design the shortest wall to comply with the Eurocode 7 Design Approach 1 partial factor sets against ULS failure. You should then determine a suitable wall section and associated cost per unit width (in plan) of wall. SLS considerations do not need to be considered in this exercise, but would normally be carried out for any design. The design is to be carried out using LimitState:GEO. You may assume that the anchor tendon and anchor plate contribute negligible extra cost, so you can design these to provide the largest support forces required for optimal wall design, but you should not design the anchor system to be bigger than required. Therefore you do not need to cost the anchor system, but you should determine the following required parameters for the final design: • shortest vertical length of anchor • shortest horizontal connection length between wall and anchor • lowest anchor/wall connecting tendon tensile strength. A good general approach for an unfamiliar problem such as this is to: 1 CIV350 Geotechnical Design Coursework 21/22 1. Do some trial and error runs using the software, changing a few parameters to get a feel for the problem. 2. Take a step back from the software and think about the mechanics of the problem. Can you break the solution down into a few stages that do not require a large number of model runs? 3. Double check you have set all fixed parameters correctly. Carry out the parametric study on the other parameters. 4. Review and sense check the final design. Hint: while you have three parameters to optimise simultaneously, you can make beneficial use of the order of priority. In principle and with careful thought and planning, you should be able to determine the optimum configuration using between 15 and 20 runs of the software. In practice you will probably use more runs than this due to trial and error. Part II: parameter/assumption variation The pile section and length chosen in Part I may be regarded as your final design. In Part II, you are to investigate the effects of the following assumptions on the required length of the pile for discussion only. These are to be investigated independently of each other. (You may increase the capacity of the anchor system as required, but it is not necessary to report any changes to the anchor system in this Part). 1. The design in Part I is to be carried out on the assumption of a specific wall/soil friction coefficient (see Section 3). Determine the impact on the design if the coefficient was not this value. Consider a range of credible values. 2. In conventional hand calculations, the earth pressure above the anchor connection point is assumed to be active. In the LimitState:GEO model (assuming a sufficiently large anchor system), the anchor connection point will be fixed and the wall is expected to rotate about this point. Therefore conditions closer to passive are modelled above the anchor. In reality the anchor system and/or pile will have some flexibility which will are likely to reduce the earth pressures above the anchor connection point. In a ULS model, this effect may be approximated by reducing the bending strength of the wall above the anchor connection point to limit the earth pressure that can be exerted at the top of the wall. Investigate the effect on the required length of wall. For more detailed guidance on how to do this in the software, see the notes in Section 4.8. 3. Anchored walls of this nature often lead to very small embedment depths. These are quite vulnerable to small changes in geometry which is not necessarily covered by partial factors on actions or strengths. Determine the geometrical margin of safety in this case. To do this, model your final design with unit partial factors and determine (i) the reduction in wall length required to cause failure, and (ii) the reduction in excavation level required to cause failure. 2 Project assessment and submission details Please refer to the CIV350 Blackboard coursework folder. 1. Following Part I you are required to submit the following information via the link in the Black- board Coursework folder (only these four numerical values are required at this stage): • wall length (m) • wall strength (kNm/m) • anchor length (m) • anchor tendon length (m) 2. Following Part II, the design must be written up using the provided report pro-forma (’CIV350 Report Pro Forma.docx’). This is designed to help you think about the issues in 2 CIV350 Geotechnical Design Coursework 21/22 the design and how to present your results. It provides a breakdown of how the marks are allocated. The focus is on the results and discussion of the results rather than asking you to put together a high quality report from scratch. However do remember that the report must be clear and easy to follow. 3 Problem parameters and notes Relevant parameters are as follows: • The soil is a sand. You have been given the following characteristic properties: – Critical state strength: cohesion intercept c′ = 0; angle of shearing resistance φ′ = 30o. – Unit weight γ = 15.5 kN/m3. The wall should be designed using critical state parameters. • The interface angle of friction δ′ between the sheet pile wall (and the deadman anchor) and the adjacent soil should be assumed to be 0.75φ′ where φ′ is the critical state angle of shearing resistance of the adjacent soil. • The anchor tendon must be connected to the wall at a point between 1.0m and 2.0m below the wall top. The anchor tendon must be horizontal and ideally connect to the anchor at mid-depth (however it may be necessary to extend the anchor to such a depth that it is no longer possible for the tendon to connect at mid-depth). The anchor plate may not be further than 25m from the wall. For simplicity it is not necessary to calculate the strength of the anchor plate. It can be assumed to be rigid. The design must also allow for the following factor: • It is possible that a surcharge load of up to 15kN/m2 could be applied over any width or series of separate widths on the horizontal surface of the soil body retained by the wall, between the locations 2m to 35m from the wall top. For simplicity it is not necessary to consider the risk of over-excavation adjacent to the wall for Part I, though this would typically be carried out. Other notes: • Wall and anchor dimensions should be determined to the nearest 0.1m, anchor tendon dimen- sions to the nearest 0.5m, bending strengths to the nearest 5 kNm/m and tensile strengths to the nearest 5 kN/m. Do not get too focused on optimizing the design to the last few cms. Remember the realities of construction on site. • For the purposes of this design exercise all final calculations should be carried out using a global nodal resolution Scale Factor of 1.6 and baseline nodal spacings of 1 in solids and 0.5 on boundaries in LimitState:GEO. The latter as set as default. (Normally a final solution would be checked at a higher nodal resolution to ensure accuracy). • For the purposes of this exercise, the costs will simply be based on the weight of steel used in the piles per metre width of wall at the rate of £640/tonne. The piles that may be used are and GU6N, GU7N, GU7S, GU8N, GU8S, GU13N, GU14N, GU15N, GU16N, GU18N, GU20N, GU21N, GU22N, GU23N, GU27N (U-piles all in steel grade S320GP). An appropriate pile section should be selected from Section 1.5 of the ArcelorMittal Piling Handbook (2016), A pdf copy of this handbook may be found on the CIV350 BlackBoard pages. (NB If there is no closely matching pile section, then you must use the next nearest section that will provide stability. If no section is sufficient then state this.). • The DA1/2 partial factor sets should be applied as Input Factors using the built in ‘Scenario Manager’ in the software. 3 CIV350 Geotechnical Design Coursework 21/22 • The DA1/1 partial factors should be applied to the action effects (bending moment and anchor force). These will be provided as outputs from the software and will require manual factoring. The variant of DA1/1 where factors are applied to action effects is denoted DA1/1* • Generally optimum ULS design of any component of the system is achieved when the system failure involves failure of that component. • It may be assumed that the conditions remain dry at all times and that the water table is at great depth. 4 Modelling in LimitState:GEO 4.1 Example model An example sheet pile wall LimitState:GEO geometry can be found on Blackboard in the file ‘an- chored wall example.geo’. Wall properties have been set arbitrarily. Check and modify as required so that the model geometry, loading (if present) and material properties are as you require them. A brief description of the model follows. The LimitState:GEO manual (can be accessed via help in the software) should be consulted for further details on specific modelling aspects. • The sheet pile wall is modelled as an Engineered Element, which is simply a 1D object that is rigid, but allows bending at ‘Nodes’ with a preset plastic moment of resistance at these nodes. • The anchor itself is modelled as a ‘deadman’ anchor (a plate anchor) using another Engineered Element, and is connected to the sheet pile wall by an anchor tendon (e.g. steel cable or rod) which is modelled by a third Engineered Element. This is set to provide a flexible link between anchor and wall. This link is modelled such that it does not itself interact with the soil around it. Note that where it meets the wall it is necessary to model a short length of wall material along the tendon direction. This avoids splitting the wall with the weaker tendon material. • The Engineered Element has additional materials modelled on each side of it which can be used to model suitable soil/wall interface properties. In the example file, the material ’Interface’ is assigned to the sides of the wall. Its properties can be modified in the usual way. Click on the wall, anchor tendon and anchor to view the material properties in the Property Editor and check you understand the settings. (N.B. The Pullout and Lateral Factor parameters control the interaction of an Engineered Element with the surrounding soil. In this case very large values e.g. 1E+30, used for the wall and anchor, indicate that the soil interacts fully with the Engineered Element. A value of zero, as used for the tendon, indicates no interaction and that the Element is free to move through the soil with no resistance. It simply transmits tension from one end to the other). The problem may be investigated using ‘Factor Load(s)’ or ‘Factor Strength(s)’ mode. Since the aim is to optimize the design, the aim is simply to achieve an Adequacy Factor of 1.0. Generally the value of the Adequacy Factor found in the two different modes will be different, however they will always coincide at a value of 1.0. It is generally recommended to use ‘Factor Load(s)’ mode (except for specific design questions) as this is faster. (Note that for ‘Factor Load(s)’ adequacy is applied to the weight of fill behind the wall. This is an unfavourable load). For efficient design you would be wanting the anchor and wall to both be on the point of failure, thus the software may be at the transition of showing/not showing a mechanism around the anchor plate and you may need to adjust the parameters slightly to show the mechanism. (N.B. If it is showing a mechanism and you are at this point, then normally the animation will show little movement). 4.2 Model boundaries The external boundaries of the model (left hand side, right hand side and base) are arbitrary and, as a general rule, should be set so that any modelled failure mechanism is not restricted by these 4 CIV350 Geotechnical Design Coursework 21/22 boundaries, otherwise solutions will be inaccurate. However do not set the boundaries unnecessarily far out as this will affect solution time. However if the model involves a two (or more) part system (e.g. anchor and wall, as in this case), in some circumstances, only one component e.g. the wall may be involved in a mechanism. You therefore need to ensure there is enough space for a mechanism to form around the anchor if needed. The easiest way to do this is to set the model so the anchor just on the point of failure. 4.3 Setting the baseline nodal resolution Scale Factor You can access this parameter by clicking anywhere on a blank area in the viewer window. This brings up the ‘Project’ level properties in the Property Editor (right hand side of the screen). Then click on the + next to the ‘Nodal Density’ entry. You can then view and set the nodal resolution ’Scale Factor’. You should find that it was set to 1.6 in the example .geo file. 4.4 Modelling Partial Factor sets Using the Scenario Manager in LimitState:GEO it is possible to select the pre-programmed partial factor sets DA1/1 and DA1/2. Ensure all loads/self weights are specified favourable/unfavourable as appropriate. Use of the DA1/1 or DA1/2 set will apply all factors at source. Eurocode 7 requires that the final design complies with both sets of factors. Thus the design will typically be controlled by either DA1/1 or DA1/2. To apply DA1/1 factors at action effect level (this is termed DA1/1*) requires a more detailed approach including a stage where factors are applied manually (this will be explained in detail later in the module). The required process is as follows: generate a new set of input factors in the Scenario Manager by selecting ”